高熵合金突破了传统的合金设计理念,成为金属材料领域的研究热点之一。其中,FCC结构的高熵合金由于铬、镍、铝、钼、钛和其他钝化元素的含量高,呈现出优异的本征耐腐蚀性能,是目前研究最为广泛的耐蚀高熵合金体系。其在盐水腐蚀环境中的腐蚀抗性远远优于传统的耐腐蚀金属材料,如不锈钢、铜合金、镍基合金等。表2总结了现有研究较为广泛的耐蚀高熵合金和工程常用不锈钢电化学极化测试后获得的腐蚀参数。可以发现,相比不锈钢,大部分FCC结构高熵合金表现出更低的腐蚀电流密度,更高的腐蚀电位和点蚀电位,具有更好的工程应用潜力。
对FCC结构高熵合金的腐蚀机理的研究结果表明,FCC结构高熵合金和奥氏体不锈钢的腐蚀机制相似,均为电荷转移和扩散控制的混合过程。在Na Cl腐蚀溶液介质中,FCC结构高熵合金具有优异的钝化膜形成能力,易于在表层形成致密的钝化膜[9]。合金中高的Cr元素含量可大大提升钝化膜的耐蚀性能,有效抵抗腐蚀性离子的渗透。此外,FCC结构高熵合金独特的结构及特性也赋予了其一些与众不同的耐蚀特征:FCC结构高熵合金表层的钝化膜呈现明显的“高熵化”,即各组成元素的氧化物/氢氧化物,以及少量结合水,共同构成了钝化膜,且钝化膜表现为多层膜形式,Cr离子倾向于在膜的内层富集;在腐蚀介质侵蚀FCC结构高熵合金的过程中,合金元素没有发生明显的选择性溶解[14]。由此推断,在腐蚀过程中,FCC结构高熵合金可能以接近协同钝化和溶解的方式与腐蚀介质发生交互作用,从而抑制局部选择性腐蚀的发生。
除了具备优异的耐蚀性能,FCC结构高熵合金的力学性能也呈现出巨大的优化空间。目前,有关FCC结构高熵合金强化机制的研究工作已经取得了长足进展,形变强化、细晶强化、析出强化等强化措施均被证实可有效提升合金的强度[28,29,30,31,32,33]。相较而言,析出强化法因效果显著、工艺成熟度高,而最受关注。其中,代表性的成果是:分别以原位弥散析出的纳米尺度的γ'相和B2相作为强化相,实现了FCC结构高熵合金力学性能的大幅度提升,开发了室温拉伸强度为1200~1500 MPa,且塑性变形量>15%的合金体系[34,35],其力学性能满足岛礁装备的服役要求。
耐蚀高熵合金的性能很大程度上取决于合金组织结构及合金化元素种类。特别是针对合金的耐蚀性能,高熵合金的相组成、相分布及形态、成分均匀性等因素均可对其耐蚀性造成显著影响。因此,大量的研究工作聚焦于研究合金化元素及热处理工艺对FCC结构高熵合金腐蚀性能的影响规律及机理。文中也分别对这两方面的研究工作进行了论述。
合金化元素对高熵合金的耐蚀性能有很大影响。不同的合金化元素可通过改变合金的电位、腐蚀过程阴极和阳极反应的极化以及相组成与腐蚀产物膜的稳定性,进而影响到合金的腐蚀行为。
表2 FCC结构高熵合金及商用不锈钢在盐溶液(3.5%Na Cl)中的电化学参数
Tab.2 Electrochemical data of FCC high-entropy alloy and commercial stainless steel obtained from potentiodynamic polarisation testing in the 3.5%Na Cl solution
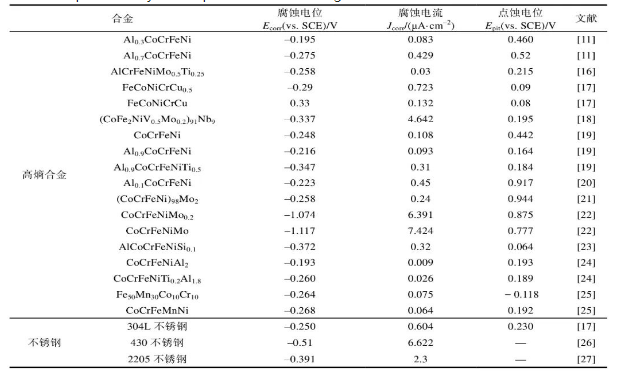
Al元素是耐蚀高熵合金中最常见的合金化元素之一。适当添加Al元素,能在合金表面形成致密的氧化膜,并改善钝化膜的稳定性,从而降低腐蚀速率,这已在Ni基耐蚀合金中得到证实。然而,在高熵合金中,与其他常见元素(如Fe、Co、Cr、Ni等)相比,Al在电偶序中的惰性较低,容易发生优先溶解。因此,Al元素的添加不利于在合金表面形成分布均匀的保护性氧化膜,相反,可能降低合金的耐蚀性能。例如,石芸竹等人[11]对AlxCo Cr Fe Ni(x =0.3,0.5,0.7)高熵合金进行了研究,发现Al的添加促进了合金相组织的转变,增加了合金中富铝相区、贫铬相区的元素偏析程度(如图2所示)。在3.5%Na Cl溶液中的动电位极化测试及腐蚀形貌观察结果表明:随着Al含量的增加,Co Cr Fe Ni Alx合金的耐点蚀能力逐渐降低,合金中腐蚀的区域主要集中于贫Cr相区。Lee等人研究Al元素对AlxCr Fe1.5Mn Ni0.5高熵合金在水环境中的腐蚀性能的影响规律时,也获得了相同的结论[36]。AlxCr Fe1.5Mn Ni0.5合金的动电位极化和电化学阻抗谱表明:随着铝浓度的增加,合金的腐蚀敏感性和点蚀敏感性增加。
Mo元素在不锈钢中的添加,可在水环境中形成Mo O42‒,吸附于合金表层,起到阻碍选择性溶解的作用,有利于提高合金的耐蚀能力。通过XPS测量和EPMA分析Fe Co Cr Ni Mox在氯化钠溶液中的腐蚀行为,可以发现,Mo的添加提高了Cr2O3/Cr(OH)3比率,并且Mo氧化物被结合到钝化膜中。与无Mo的Fe Co Cr Ni合金相比,Fe Co Cr Ni Mox高熵合金的耐腐蚀性显著提升,含Mo高熵合金的腐蚀击破电位明显较高[2]。在Co1.5Cr Fe Ni1.5Ti0.5Mox高熵合金中,循环极化测试和SEM显微分析结果也证实了含Mo合金在Na Cl溶液中不易发生点腐蚀[37]。
Ti属于热力学不稳定金属,然而在多种腐蚀介质中,Ti合金表现出极强的耐蚀性能,这与其在合金表面形成的致密Ti O2钝化膜密不可分。Han等人在对Al Cr Fe Ni Mo0.5Tix高熵合金耐蚀行为的研究中发现,合金钝化膜的稳定性随着Ti含量的增加而增加,意味着Ti的添加增加了合金耐点蚀性能[16]。然而,在Al Co Cu Fe Ni高熵合金中,大Ti原子的加入促进了FCC相的形成,但合金的耐腐蚀性能下降[38]。由于Ti容易和高熵合金其他元素形成金属间化合物第二相,例如在Al Co Cr Fe Ni Tix中形成Fe2Ti性Laves相[39],以及在Co Cr Fe Ni Tix中促进了R、σ和Laves相(如图3所示)的形成[40]。这些相的析出均会导致合金中元素的偏析,影响合金的整体耐蚀性能。
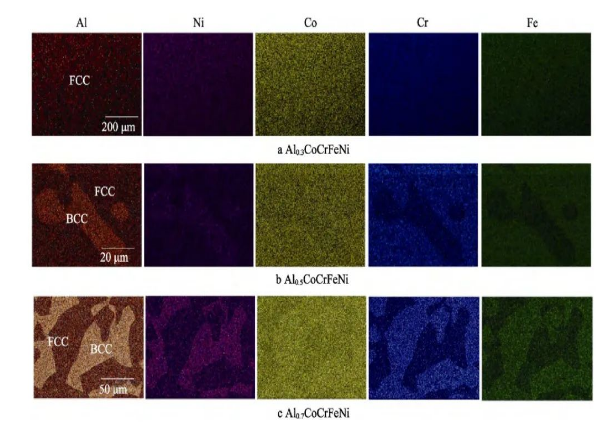
图2 高熵合金Al0.3Co Cr Fe Ni、Al0.5Co Cr Fe Ni和Al0.7Co Cr Fe Ni的X射线光谱(EDS)元素分布[11]
Fig.2 X-ray spectra (EDS) elemental distribution of (a) Al0.3Co Cr Fe Ni,(b) Al0.5Co Cr Fe Ni,and (c) Al0.7Co Cr Fe Ni[11]
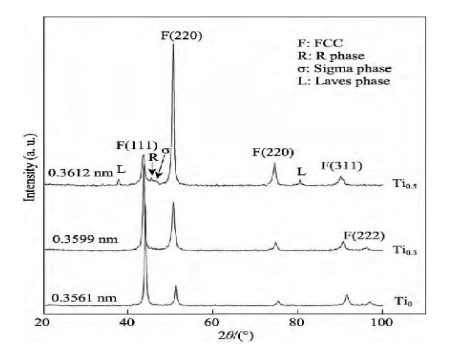
图3 Co Cr Fe Ni Tix高熵合金的XRD图谱[40]
Fig.3 XRD pattern of the Co Cr Fe Ni Tix high-entropy alloy[40]
Cu的标准电极电位比氢正,在中性盐类的溶液中,特别是含氧时,铜可钝化,具有良好的耐蚀性。Hsu等人[17]研究了Fe Co Ni Cr Cux高熵合金在3.5%Na Cl溶液中的腐蚀行为,如图4所示。由于合金中富铜枝晶和贫铜(富铬)枝晶间形成具有明显电位差的电偶作用,加速了合金的腐蚀,铜含量的增加也增加了合金局部腐蚀的趋势。另外,含铜高熵合金表面的腐蚀类型主要为局部腐蚀和点蚀,而不是均匀腐蚀。尽管Cu的添加会增加Fe Co Ni Cr合金中元素的偏析,影响合金的耐蚀性能,然而Zhou等人[41]利用铜的抗菌作用,设计了一种具有抗菌的新型Al0.4Co Cr Cu Fe Ni高熵合金。研究表明,合金中溶解释放的高浓度铜离子有效阻止了生物腐蚀性海洋细菌物种的生长和生物膜的形成。
Nb是活性金属,在表面自发钝化形成的氧化膜在许多强腐蚀的化学条件下仍然非常稳定,因此,Nb作为合金化元素在奥氏体不锈钢中有广泛的应用。Li等人[18]研究了加入Nb元素对无铬的(Co Fe2Ni V0.5Mo0.2)100-xNbx共晶高熵合金耐蚀性能的影响,发现在3.5%Na Cl溶液中含9%(原子数分数)Nb的共晶合金具有最佳的耐蚀性能。在Co Cr Fe Ni合金中,加入11.2%的Nb时,合金可形成纳米结构共晶高熵合金。该合金在1 mol/L Na Cl中显示出卓越的防腐蚀和再钝化能力,优于各种传统合金和其他高熵合金,合金表面形成致密的非晶钝化膜能有效防止点蚀的发生[13]。另外,Wang等人[42,43]分别通过等离子喷涂和激光熔覆在碳钢上制备出的(Co Cr Fe Ni)95Nb5高熵合金,在3.5%Na Cl溶液中具有良好的耐腐蚀性。
到目前为止,通过研究合金化元素对高熵合金进行耐腐蚀性能的影响发现,合金化元素的加入不仅可以改变合金表面钝化膜的成分组成,增强合金的耐点蚀能力,但也可能促进高熵合金微观结构变化,甚至导致严重的元素偏析或金属间化合物的形成,这往往不利于合金耐腐蚀性能的提高。因此,还需进一步明确不同合金化元素含量对高熵合金微观结构与耐蚀性之间的相关性,为耐蚀高熵合金的设计和开发奠定理论基础。
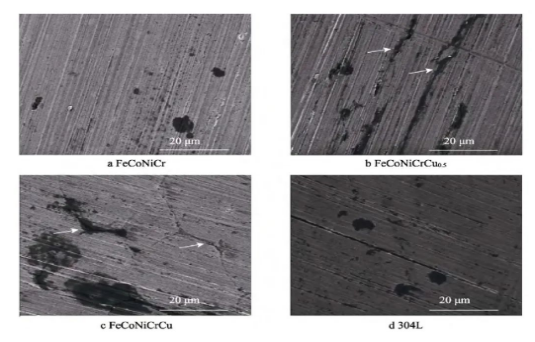
图4 在3.5%Na Cl溶液中浸泡30 d后合金的表面形貌[17]
Fig.4 Surface appearances of alloys after immersion tests in 3.5%Na Cl solution for 30 d[17]
高熵合金的组织结构及化学成分的不均匀是导致高熵合金耐腐蚀性能降低的重要原因之一。通过热处理工艺,可以消除合金中的内应力,粗化晶粒,促进第二相析出或溶解,改变合金相的形貌、大小和分布,加速组元再分配,从而影响合金的电化学行为。因而,合理控制热处理工艺,可以有效提升高熵合金在盐水溶液中的耐腐蚀性能。
目前,多采用退火处理和时效处理的方式,优化耐蚀高熵合金的微观结构和耐蚀性能。Zhang等人[44]研究发现,对Al Fe Ni Co Cu Cr高熵合金进行1000℃、保温3 h的退火处理后,退火态合金在3.5%Na Cl溶液中显示出了较铸态合金更加优异的耐蚀性能。电化学测试结果表明,铸态和退火态高熵合金的腐蚀电位分别为‒237.36、‒215.36 m V,腐蚀电流密度为2.1632×10‒4、1.3011×10‒4 A/cm2。与铸态合金相比,退火态合金的电化学性质更加稳定,合金的腐蚀形态由晶间腐蚀结合点蚀形态转变为单点蚀形态,且退火态合金的点蚀密度明显降低。由此可见,退火处理可以显著改善高熵合金的耐蚀性能。
研究发现,热处理温度是影响耐蚀高熵合金耐蚀性能的关键因素。Wang等人[21]研究了热处理温度变化对高熵合金耐蚀性能的影响规律。经700℃和900℃时效处理后,(Co Cr Fe Ni)100‒xMox合金在3.5%Na Cl溶液中的极化曲线和电化学阻抗谱表明,随着时效温度的增加,合金的耐蚀性逐渐提高。此外,通过对Al0.3Cr Fe1.5Mn Ni0.5合金进行650℃和750℃保温8 h热处理,合金的耐腐蚀性能也显著提高[45]。主要归因于退火处理促进了Al-Ni相和σ相的析出,导致基体中Cr含量的升高,进而提升了基体的耐蚀性能。但随退火温度升高,该合金点蚀敏感性增加。
热处理时间对高熵合金的耐蚀性能也有显著影响。北京科技大学的Shi等人[11]研究发现,对AlxCo Cr Fe Ni高熵合金进行不同时间的退火处理后,由于化学成分偏析造成的合金局部腐蚀行为得到了不同程度的缓解。在1250℃退火温度下,将退火时长由50 h提升至1000 h,高熵合金基体的组织结构更加均匀,同时合金成分偏析现象减弱,合金的功函数变化减小,耐腐蚀性能显著提高。经长时间退火处理后,高熵合金在盐水溶液中的腐蚀行为得到了明显的控制,如图5所示。