腐蚀是钢铁材料服役过程中普遍存在的失效问题。据不完全统计,每年因腐蚀造成的经济损失占国内生产总值(GDP)的3%左右。所以,各国都非常重视开发耐大气腐蚀性能的钢铁材料技术。耐大气腐蚀钢(以下简称耐候钢)是指在钢中加入一定量的合金元素,如P、Cu、Cr、Ni等来提高钢在大气环境下的耐腐蚀性能。早在1900年,欧美科学家发现Cu能够改善钢在大气中的耐腐蚀性能。1933年美国钢铁公司首先研发出Cor-Ten系列耐候钢,主要用于制造铁路车辆[4]。Cor-Ten钢的力学性能比普碳钢提高30%,耐腐蚀性能显著提高。1941年,首个耐候钢标准(ASTMA-242)提出;1968年,根据P含量将耐候钢细分成2类,Cor-TenA((0.07%~0.15%)P,质量分数,下同)及Cor-TenB(≤0.04%P)[5,6]。1992年,美国联邦(FHWA)、美国钢铁协会(AISI)及美国海军共同开发了高强钢(HPS)用于桥梁建筑。HPS通过降低C、P及S含量提高可焊接性能、提高Mn含量上限改善断裂韧性及屈服强度、形成保护性锈层来提高耐腐蚀能力[7]。新日本制铁公司后来从美国钢铁公司引进了Cor-Ten系列耐候钢,并开发出多种场合应用的耐候钢。自此,耐候钢在欧美、日本等国家的建筑设施、桥梁、车辆等方面得到广泛应用。
我国于20世纪60年代起开始深入研究耐候钢,目前已研发出多种耐候钢,主要有:低P含Cu、Cr、Ni的耐候钢,高P含Cu、Cr、Ni的耐候钢(09CuPCrNi-A和09CuPCrNi-B),高P含Ti的耐候钢(09CuPTiRE-A和09CuPTiRE-B)以及高P含V的耐候钢(08CuPVRE)等。我国庞大数量的钢铁材料应用的腐蚀失效问题,特别占总钢产量约70%的普碳钢很容易被腐蚀导致服役失效,是急需解决的重要问题。表1列出了20世纪耐候钢的发展历程。
钢在大气中的腐蚀是涉及多种发生在气相、液相和固相界面的化学、电化学和物理过程,其腐蚀主要以电化学腐蚀为主。钢表面在大气环境中凝结一薄层液膜,伴随着液膜中溶解CO2、SO2、NOx、H2S、NH3等气体及盐离子(如Cl-)等,形成电解质溶液使得阳极发生溶解,液膜中的H+或O2-在阴极上被还原,推动电化学的发生。与不锈钢不同,耐候钢并不形成致密的极薄钝化层,而是通过与周围介质不断的交互作用,经过一段时间在钢表面形成稳定化锈层,极大程度延缓钢的进一步锈蚀。
耐候钢具有良好的耐腐蚀能力,合金元素起到决定性作用,主要体现在3个方面[8]:(1)合金元素降低锈层的导电性能,影响锈层中物相结构和种类;(2)加速钢均匀溶解,促进Fe2+向Fe3+转化,推迟锈的结晶;(3)阻塞裂纹,减少相关缺陷。其中,Cu作为耐大气腐蚀钢中最有效的合金元素,对其改善钢的耐大气腐蚀性能的作用机理主要有2种观点:一种是Cu能够促进钢阳极钝化,降低腐蚀速率;另一种是Cu在基体与锈层间富集,形成以Cu、P为主与基体紧密结合的保护层。P元素作为阳极去极化剂,与Cu配合,可加速钢的均匀溶解,促进Fe2+向Fe3+转化,有助于形成均匀的锈层。Cr元素能在钢表面形成致密的氧化膜,提高钢的钝化能力。研究[9]认为,提高Cr含量有利于细化α-FeOOH,有效抑制腐蚀性Cl的侵入。Ni元素使钢的自腐蚀电位向正方向变化,增加了钢的稳定性。Ti及V元素的加入,更多是通过形成TiN或者V的碳氮化物,抑制晶粒长大,从而提高为耐大气腐蚀钢的析出强化和晶粒细化强化效果;稀土(RE)元素是极其活泼的元素,在钢中加入有利于净化钢液,细化枝晶,改变夹杂物性质、形态和分布,减少腐蚀源点,从而提高钢的性能,也可有效提高P、S、Cu等元素溶质非平衡分配系数。
耐候钢裸露在大气环境下,最初会形成与普碳钢一样的锈层,但经过3~5a的环境腐蚀,靠近基体的锈层不断溶解再析出形成较为致密的非晶态羟基氧化物[10]。最终经过多年后,耐大气腐蚀钢形成稳定的锈层,其中起主要保护作用的内锈层是富集了Cr、Cu、Ni、P等元素的α-FeOOH,如图1所示。
钢铁材料的耐大气腐蚀是一个与介质、温度、时间、空间、地域等因素相关的非常复杂的问题,现在的研究工作更多的还是实验现象的总结,并据此开发出相关的耐候钢技术。在现象、规律与机理研究等方面还有大量工作需要开展。
表1 20世纪耐候钢的发展历程
Table 1 Brief history of weathering steels in 20th century
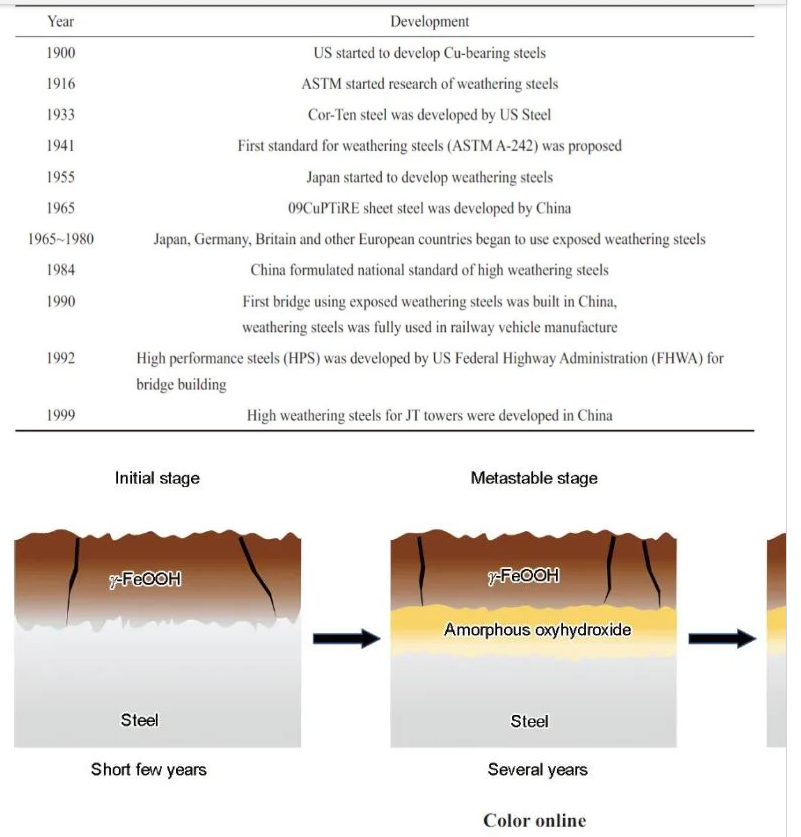
图1 耐候钢锈层转变示意图
Fig.1 Schematic progress for stable and protective rust layer formation on a weathering steel
稀土元素在钢中的应用一直受到关注,也有过起伏,近年又开始被人们重视起来。稀土元素是指原子序数从57至71的镧系15个元素和化学性质相近的Sc、Y共17个元素。由于稀土原子性质活泼,结合力较强。概括地讲,将稀土添加在钢中可以起到改善凝固组织、改变固态相变组织、形成无害化低熔点夹杂物、通过偏聚强化界面、钝化表面锈层等作用,从而显著提高钢的韧性、耐腐蚀性能、抗疲劳性能、耐热性能等。稀土作为我国富有的战略性资源,其开发利用了大量富余的La、Ce、Y,需要寻找量大面广的应用场合,在钢铁材料中的合理应用是当今的重要课题。
稀土元素的特殊性质决定了稀土耐候钢的发展历程。由于稀土在钢液中与O、S有很强的亲和力,20世纪50年代起,稀土应用在钢液中用于脱氧和硫化物变性。20世纪70年代中后期,随着钙处理在钢中逐渐广泛使用,钙处理取代了稀土处理的脱氧与硫化物夹杂物变性作用。伴随着我国稀土开发的资源合理利用与已有的稀土合金化重新认识,近年来国内多个研究团队和钢企重新关注稀土钢的技术开发。对于量大面广的普碳钢能不能通过稀土合金化来提高其耐大气腐蚀性能是一个具有挑战性的问题。如果可以,将实现低成本提高大量钢铁材料耐腐蚀性能,形成具有中国特色的钢铁材料技术。
我们认为,大原子半径的La、Ce、Y稀土元素在钢中的赋存状态是重要的关注点。在目前的冶金状态下,稀土元素在钢中应该是以2种方式存在:(1)与氧硫化合物结合形成复合夹杂物;(2)偏聚在晶界、相界和自由表面等界面处,如图2所示。与氧硫化合物形成的稀土复合夹杂物可以改善材料的塑性和韧性,同时降低与基体的电极电位差,阻碍由夹杂物导致的点蚀发生。在晶界和相界偏聚的稀土元素可以降低界面的自由能,减轻界面高能量导致的腐蚀。偏聚在自由表面的稀土元素将起到钝化锈层的作用。
过去几十年国内外研究工作充分证明了稀土在钢中的有益作用,早期的稀土通常作为脱氧剂加入到钢液中,对钢液起到净化作用。随着钢的精炼与凝固方式的改变,现代钢铁中的O、S含量控制较好,稀土在钢中的主要作用更偏向于改变夹杂物的性质及状态以及稀土微合金化。在Q235普碳钢和09CuPCrNi耐候钢中分别加入一定量的稀土(其中Q235RE含14×10-6Ce和30×10-6La,09CuPCrNiRE含300×10-6Ce和110×10-6La)并进行比较,发现夹杂物形貌及尺寸均发生显著变化[11]。稀土合金化前,Q235及09CuPCrNi钢中的夹杂物以MnS以及Al2O3为主,尺寸在3μm左右,形状不规则,与基体结合不紧密,部分夹杂发生脱落。稀土合金化后,夹杂物由不规则块状转变为球状,且夹杂物尺寸减小至0.5~1μm。稀土合金化后,Q235及09CuPCrNi钢中的夹杂物分别转变为稀土-氧硫化物及稀土-硫化物。说明钢中加入适量稀土元素后,夹杂物发生改性,转变为尺寸更小的球状稀土夹杂物,其主要原因是稀土夹杂物的形成能较低[12]。
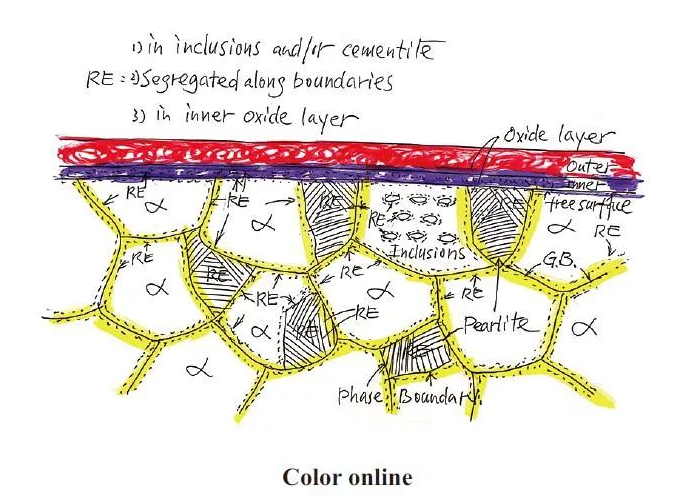
图2 稀土元素在钢中赋存示意图
Fig.2 Schematic of the occurrence of rare earth ele‐ ments in steel (RE — rare earth, G.B. — grain boundary)
而稀土夹杂物的转变,显著提高了钢的抗点蚀能力。Liu等[11]研究中的阻抗图中显示,稀土的加入增大了容抗弧的半径。低频时出现的电感收缩现象表明钢处于点蚀诱发的阶段,溶液中的阴离子SO4-等在电极表面富集从而发生点蚀。添加稀土后的容抗弧半径明显增大,说明稀土元素提高了钢抗点蚀能力。采用等效电路图对阻抗谱进行拟合,结果表明,稀土合金化后的电荷转移电阻明显提高,说明稀土可有效降低腐蚀倾向,阻碍电荷在电极表面双电层间的转移,抑制电极反应的发生,从而提高耐腐蚀性能。钢中的非金属夹杂物是点蚀主要的诱发源,尤其是MnS和Al2O3夹杂物。MnS夹杂物与钢基体之间存在腐蚀微电池,MnS是良导体并且电极电位比Fe要高,在腐蚀系统中充当着阴极的作用,而基体作为阳极会先发生溶解;另一方面夹杂物与基体结合处氧化膜薄弱,很容易受到侵蚀性离子的破坏,使周围基体处于活化状态,优先发生溶解产生Fe2+,随后Fe2+发生水解产生H+,造成了夹杂物与基体界面处局部酸化,pH值降低,促进了MnS夹杂物的溶解,诱发了点蚀的发生和扩展。钢中加入稀土后,尺寸较小的球状稀土夹杂物减小了与基体的接触面积,进入活化状态的基体减少,活化面积减少,从而减弱了夹杂物与基体之间的微区电化学腐蚀,使钢的耐点蚀能力提高[13]。
采用周期浸润腐蚀实验,实验溶液为0.01mol/LNaHSO3水溶液,实验温度为45℃,相对湿度为70%。周期浸润循环时间为60min,其中浸润时间为12min,暴露时间为48min,腐蚀时间为24、48、96及144h。如图3所示,稀土合金化后的Q235及09CuPCrNi钢的腐蚀速率均有明显降低,其中Q235钢加入稀土后的腐蚀速率与未加稀土的09CuPCrNi钢腐蚀速率相当。仅仅在普碳钢中加入少量稀土就可达到与加入多种耐蚀元素的耐候钢相近的抗腐蚀效果,而稀土合金化后的Q235RE钢的经济成本显著低于09CuPCrNi钢,因此,稀土对钢耐蚀性能的提高作用不可忽视。
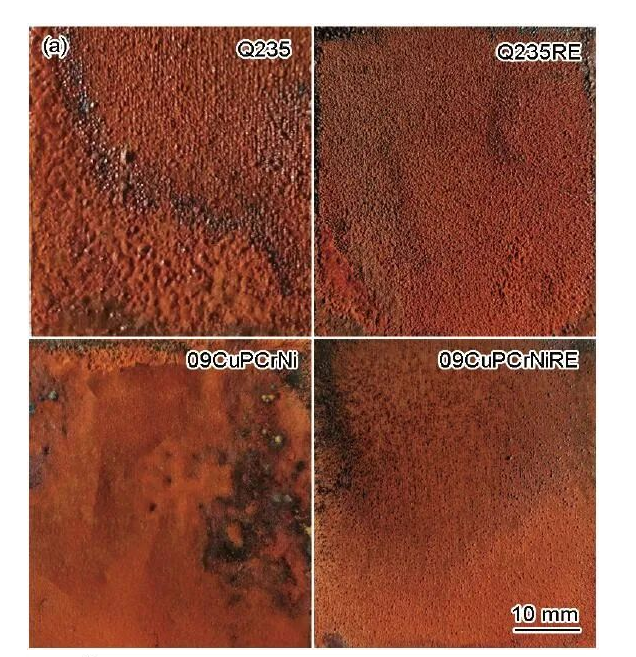
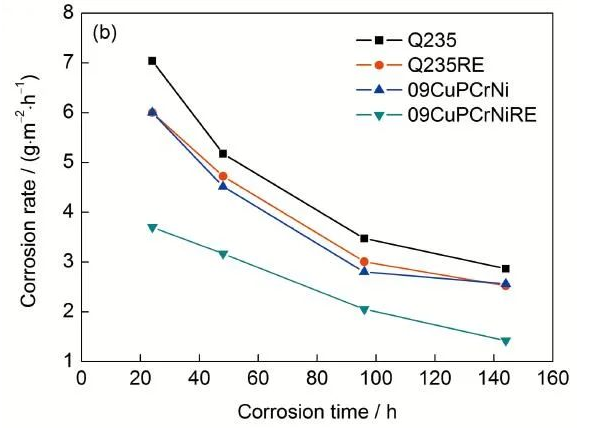
图3 添加稀土前后的 Q235 和 09CuPCrNi 钢周期浸 润腐蚀144 h后的样品形貌及腐蚀速率
Fig.3 Corrosion morphologies after dry-wet cycle test for 144 h (a) and corrosion rate during immer‐ sion test (b)
实验结果表明,稀土使钢耐腐蚀性能显著提高,而稀土在钢中的赋存状态和踪迹也至关重要。由于RE与Fe的原子半径相差较大,RE作为表面活性物质时,主要偏聚于晶界处,能够显著降低界面张力、晶界能以及晶界迁移驱动力。以Ce原子为例,如图4所示,通过在深冷条件下制备了沿晶断口,采用Auger电子探针(AES)从晶界向晶内进行深度溅射,观察RE特征峰的变化。结果表明,在溅射初期(溅射时间为0和0.5min时),断口表面由于轻微氧化,O含量较高但并未发现Ce原子富集现象。当溅射时间为1min时,O含量明显下降,表明溅射束已穿透氧化层到达晶界,同时出现了较明显的Ce原子的特征峰值。随着溅射时间继续延长,Ce原子的特征峰值再次消失,此时已经溅射到晶内。因此证明Ce原子确实向晶界偏聚,偏聚层非常薄,根据离子溅射参数估算,RE原子的偏聚层只有几个原子层的厚度。
除此以外,对盐雾实验72h后的锈层通过电子探针(EPMA)进行元素分析,发现在锈层与基体的界面处出现了稀土元素的聚集。说明在耐大气腐蚀钢锈层的形成过程中,RE原子会向锈层与基体结合的界面处迁移,提高了锈层和基体的结合力,增强了锈层的致密性,阻碍腐蚀性Cl进入,减缓基体的进一步腐蚀。但RE原子究竟是存在于锈层中还是基体中尚需要深入研究。
已有的基础理论研究与生产实践均证明,稀土合金化是提高钢铁材料耐腐蚀性能的有效方法之一。稀土钢发展至今的主要问题在于:稀土合金化机理尚有待深入研究,相关的技术质量控制方向不明确;稀土有效加入方法与稀土合金元素收得率不高。上述问题可能导致稀土元素在钢中不仅没有起到有利作用,反而成为有害夹杂物,造成连续生产过程的间断。“稀土,稀土,稀里糊涂”是我国稀土耐候钢开发中的真实写照。深入探索稀土在钢中的赋存与踪迹以及作用机理成为亟需解决的基础科学问题。探索新型稀土加入方法,保证稀土元素在钢中的收得率不低于70%,保证生产过程连续顺行,才能形成工业化的稀土合金化技术。我们的研究表明:稀土在钢中与氧硫化物结合可变性夹杂物,在各种界面偏聚提高界面性能。在目前先进的冶金生产工艺流程条件下,在科研人员的努力下,有望很快解决上述问题。结合中国富余的La、Ce、Y稀土资源,在量大面广的普碳钢中通过稀土合金化,普遍低成本地提高钢材的耐大气腐蚀性能,可实现钢铁材料的减量化使用,形成具有中国特色的钢铁材料技术。
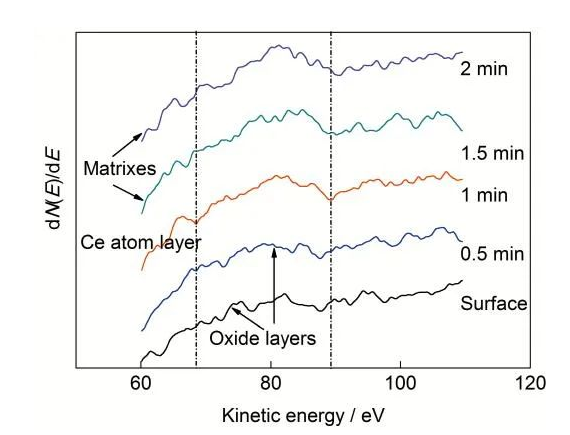
图4 09CuPCrNiRE钢中Ce元素的AES谱
Fig.4 AES spectra of Ce in 09CuPCrNiRE steel