表面工程通过表面涂覆、表面改性或多种表面技术复合处理,改变固体金属表面的形态、化学成分、组织结构和应力状况,以获得表面所需性能,如耐磨、耐蚀性能。因此,表面工程技术成为改善金属材料动态耐磨防腐的首选技术途径,合理的表面技术可极大地提高传统材料的服役期限,拓宽传统材料的应用范围[34-37]。基于此,针对金属材料的腐蚀磨损耦合损伤问题,通过在材料表面进行涂覆及改性处理,可将金属和涂层的优点相结合,使金属材料具有优良的综合机械性能,延长使用寿命。针对不同的表面工程技术,本文综述了PVD硬质涂层技术、热喷涂涂层技术及聚合物粘结涂层技术与电镀涂层技术改善金属材料的动态耐腐防腐行为。
深海或远海机械系统维护补给困难,因此相关部件的可靠性与稳定性要求高,须通过耐磨与防腐一体化防护技术进行强化处理。研究者们针对PVD涂层,如Cr N、Ti N、GLC等,通过研究磨损-腐蚀交互作用机制,构建具有致密结构、多层界面的高承载及腐蚀通道阻隔作用的涂层材料,研制了一系列集低摩擦、耐磨损与防腐蚀特性于一体的抗磨耐蚀材料,有效改善了金属材料的抗磨蚀性能,如表2所示。
PVD涂层的硬度较金属材料有显著提高,如Cr N涂层的维氏硬度约为2000HV,Ti N涂层的约为2800HV,类金刚石的约为2500HV,均较316L、2205双相钢的硬度(不超过300HV)有明显提高。因此,根据材料硬度与耐磨性的正比关系,可推测具有高硬度特性的PVD耐磨与防腐一体化涂层可显著提高金属材料的机械磨损抗力。研究结果表明:对于Cr N涂层,机械磨损占总腐蚀磨损损失的41.2%,较金属材料有显著提升[38]。基于此,提高材料硬度是改善金属材料机械磨损的有效途径。
进一步对不同体系PVD耐磨与防腐一体化涂层进行对比分析。Lei Shan等发现Cr N、Ti N及GLC涂层均有效改善了金属材料的相关性能,如316L不锈钢的腐蚀磨损性能。对于Cr N体系的涂层,其中Cr2N/Cr N结构的涂层在海水中具有更加优异的润滑减磨作用[38-42]。此外,C、Si元素的加入均降低了Cr N涂层的摩擦系数及磨损率,尤其当Si元素质量分数为1.44%、C元素原子数分数为5.72%时,Cr N体系涂层的摩擦磨损性能得到了显著改善。因此,三元及四元体系Cr N涂层可为改善金属材料的腐蚀磨损性能发挥重要作用。
表2 PVD耐磨与防腐一体化功能涂层的腐蚀磨损耦合损伤[38-48]
Tab.2 coupled damage of corrosive wear of
integrated PVD anti-wear and anti-corrosion functional coating
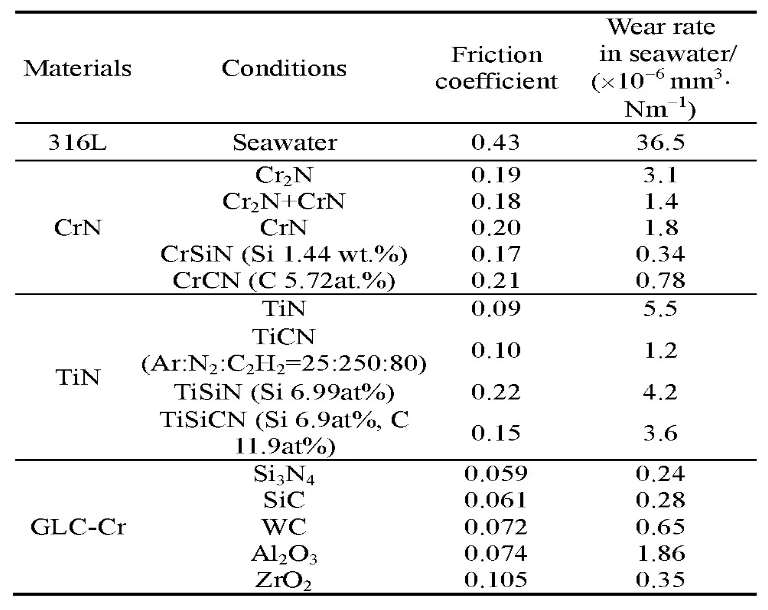
Ti N涂层是一种在刀具、模具等行业获得广泛应用的通用型PVD涂层,可以提高材料的硬度并具有优异的耐腐蚀性。Lei Shan等考察了一系列Ti N涂层在海水环境中的腐蚀磨损性能,结果表明Ti N体系涂层同样可用于改善海水环境中金属材料的腐蚀磨损性能,如表2所示[44-46]。Ti CN和Ti Si N相比于二元Ti N具有更加优异的抗磨蚀能力,尤其是C元素的加入显著提高了Ti N涂层的磨损抗力。其次,四元Ti Si CN涂层的腐蚀磨损性能,随着C元素的加入,较Ti Si N涂层有一定改善。因此,三元或四元Ti N涂层较二元Ti N涂层更适宜于海水环境运转部件的应用。
GLC薄膜指一种以sp2杂化结构为主的高度无序态非晶镶嵌细小石墨团簇结构的碳基薄膜,在水环境中,该体系薄膜比DLC具有明显的优势。基于GLC在水环境中具有优异的摩擦学性能和良好的自润滑性能,Chunting Wang等研究了GLC薄膜与不同配副在海水环境中的摩擦学行为,如表2所示[47-48],结果表明GLC薄膜与陶瓷球的摩擦系数为0.06~0.11,其中Si3N4/GLC的摩擦配副磨蚀性能表现出明显优势,且磨损表面较光滑、平整,未出现金属配副的粘着和局部撕裂磨损。因此,GLC薄膜有望为以海水为工作介质的海工装备表面防护提供一条新途径,以推进海洋强国战略的顺利实施。
镍基涂层因以金属镍为主而具有优异的耐腐蚀性能,但存在硬度低、耐磨性差等问题。因此,人们利用等离子喷涂设备制备WC陶瓷增强镍基复合涂层,并研究了涂层在海水工况下的磨蚀性能[49-50]。其中,WC增强镍基复合涂层主要由灰色的连续相和白色的带状相组成,分别为γ-Ni固溶体和碳化钨。海水工况磨蚀测试表明,WC增强镍基复合涂层的摩擦系数和磨损率均优于316L不锈钢,尤其在干摩擦条件下,其磨损率甚至比316L不锈钢低两个数量级左右。这表明WC陶瓷增强镍基复合涂层具有良好的耐磨蚀性能,可以作为316L不锈钢的表面防护的一种重要手段。
作为典型的电镀涂层,镍镀层在现代工业获得了广泛应用,同样有望解决金属材料的耐磨蚀问题[51-52]。研究表明:随着晶粒尺寸从50 nm减少至5 nm,镀层的耐腐蚀性能增强,非晶镍镀层的耐腐蚀性能达到最好;非晶纳米晶涂层的耐腐蚀性能介于20 nm镀层与5 nm镀层,显示了比大尺寸纳米晶优越的耐腐蚀性能。此外,不同晶粒尺寸镍镀层的硬度为:5 nm>非晶/纳米晶>非晶>20 nm>50 nm。因此,晶粒细化和非晶化可提高镀层的硬度及耐腐蚀性。
通过设计力学性能优异且耐高温、耐化学腐蚀的改性高分子树脂,经高硬度、耐磨陶瓷颗粒筛选和级配,结合碳纤维、聚醚醚酮纤维、石墨烯、碳化硅、氮化硼等功能填料的优异力学和防腐性能,可实现协同耐冲蚀防腐功能。
3.5 展望
综上所述,建设海洋强国,离不开强大的海洋国防及全方面海洋资源的开发利用。鉴于海洋装备长期处于海洋腐蚀性环境中,关键摩擦副将难以回避海洋环境下的腐蚀与磨损耦合损伤失效问题。而海洋等腐蚀性环境服役的工程装备的长寿命安全运行,离不开传输、传动、连接、密封机构的长寿命稳定运行,此类机械的工作面除受到海水的腐蚀作用外,相对运动也必然会引起摩擦磨损现象的发生。因此,研究腐蚀与摩擦的交互作用机理、海洋环境动态变化下的长效可靠性及耐磨防腐一体化技术极其重要。通过加强涉海装备关键性的典型机械零部件的磨蚀研究,积累现场数据,并结合实验室模拟及仿真技术,加强磨蚀机理研究,阐明腐蚀性介质的p H值、温度、速度等因素在磨蚀中的作用规律都是重要的研究方向。此外,金属材料如316L不锈钢、2205双相不锈钢的机械磨损分量约占总损失量的70%,钛合金、镍合金、铝合金的机械磨损分别约占总损失量的63.7%、71.5%、80.2%。因此,针对金属材料的腐蚀磨损失效中机械磨损为主要损伤因素的前提提出针对性的防护技术,研究耐磨与防护一体化材料及材料磨蚀的控制机理,是提高在腐蚀介质中服役的装备运行可靠性、稳定性的基础性工作。
上述研究表明,耐磨与防腐一体化涂层的选择应参考如下准则:(1)材料体系耐氯离子腐蚀;(2)钝化层形成速度快;(3)避免疲劳磨损;(4)具有较好的耐磨性。其中,耐氯离子腐蚀包括陶瓷相、镍、铜、钛等,同时钝化层在破损后易于修复。此外,非晶/纳米晶化是实现强耐磨抗蚀一体化功能的主要途径,如纳米化电镀镍基涂层、非晶/纳米晶复合Cr N基涂层材料、铁基非晶涂层等,均在海水环境中有优异的表现,成为抗磨蚀的重要材料之一。