不锈钢,如304、316L、2205双相不锈钢等金属材料,因具有优异的耐腐蚀性能和机械性能而成为海洋装备不可或缺的结构材料,如设计使用寿命达120年的港珠澳大桥即采用2205双相不锈钢作为主体钢结构[16-17]。在腐蚀性环境中,该类材料表面易于形成致密的钝化膜而具有优异的腐蚀抗力。但是,在力学-电化学耦合作用下,材料表面的钝化膜容易因擦伤而破坏,加剧材料的损伤。因此,研究不同腐蚀磨损影响因素对海水环境中金属材料腐蚀磨损行为的影响,阐明材料的耦合损伤机理,对于海洋的开发和利用具有重要意义。
奥氏体不锈钢(如304、316L不锈钢)因具有优异的耐氯离子腐蚀能力,而在海洋环境中获得了广泛应用。因此,考察不锈钢的腐蚀磨损行为及失效机理,可为不锈钢在腐蚀性介质中的服役安全提供依据[18-22]。Yue Zhang的研究表明,海水环境摩擦中,具有低层错能的奥氏体304不锈钢易于在摩擦应力作用下发生马氏体相变,高硬度的马氏体相改善了不锈钢的耐磨性,但相变反过来加剧了摩擦接触面的电偶腐蚀等,从而形成了腐蚀与磨损的协同作用(见图3)。因此,摩擦与磨损过程促进了不锈钢材料的宏观电偶腐蚀的发生,加剧了材料的腐蚀倾向,宏观电偶腐蚀所形成的疏松产物反向加剧了材料的磨损。摩擦与磨损的应力过程诱导磨损表面生成了马氏体相,所生成的马氏体相具有高硬度、高耐磨性,抑制了磨损的加重。但是,磨损表面生成的马氏体相与奥氏体基体相所组成的微观电偶腐蚀加剧材料的腐蚀,微观电偶腐蚀造成马氏体溶解,导致磨损表面的马氏体反复处于生成/溶解过程。磨损与腐蚀过程促进了微观电偶腐蚀的发生,微观电偶腐蚀导致马氏体相溶解,加剧了材料的磨损。
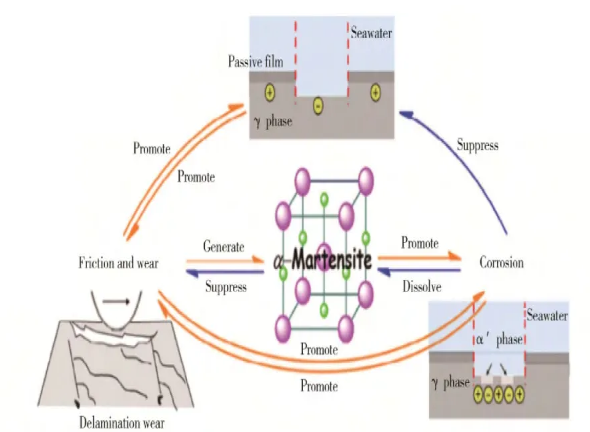
图3 304不锈钢腐蚀磨损过程中马氏体相变机理[18]
Fig.3 Mechanism of martensitic transformation during
corrosive wear of of 304 stainless stee[18]
朱禄发[23]进一步考察了载荷对316L不锈钢、2205双相钢海水腐蚀磨损和阴极保护条件两种常用的海水工况下的腐蚀磨损行为,结果表明:海水腐蚀加速了不锈钢的材料损失,而合适的阴极保护则改善了材料的抗磨蚀性能。腐蚀磨损过程中,海水腐蚀磨损导致不锈钢发生马氏体转变,而产生的马氏体和未转变的奥氏体组成了微观电耦合,从而改变了表面钝化膜的特性和稳定性,降低了不锈钢的耐腐蚀性能。与316L相比,2205双相钢具有更低的磨损率和优异的耐腐蚀性,更适合应用于海水腐蚀磨损环境。同样在腐蚀磨损过程中,2205钢发生了σ相变、位错及晶格偏移等微观结构变化,其中金属间化合物σ相的形成导致贫Cr(Ni)区的出现,引发微观电偶腐蚀,加剧了材料的腐蚀损伤和腐蚀对磨损的促进。
因此,以奥氏体不锈钢为例,摩擦诱导作用下,材料的微观结构及相组分的改变起到了应变强化的作用,从而提高了材料的抗磨损能力。但是,磨损区域与未磨损区域、相变区域与稳定区域的微观电偶腐蚀,加剧了材料的腐蚀损伤及腐蚀对磨损的促进作用。基于此,根据服役工况设计运动部件的接触面、调控服役工况、选择适宜的材料是提高海工装备关键运动部件服役安全的重要途径。
Yue Zhang进一步研究腐蚀介质浓度、p H值对304不锈钢腐蚀磨损耦合损伤行为及机理的影响[24-25],结果表明:高浓度的氯离子导致304不锈钢的局部腐蚀敏感性显著增大,尤其是点蚀敏感性,从而增大了304不锈钢静态和磨蚀过程中的腐蚀损伤。然而,随着氯离子浓度的升高,304/Al2O3摩擦体系的摩擦系数和磨损率均出现了明显降低,且磨损表面趋于光滑,表明氯化物溶液的良好润滑性减弱了腐蚀对磨损的影响。因此,提高腐蚀性溶液的浓度,如增加海水中的氯离子,可大幅降低腐蚀磨损过程中的纯机械磨损和腐蚀对磨损的促进作用,该研究可为金属材料的耐磨抗蚀提供新思路。
其次,随着p H值(7.2~9.2)的升高,304/Al2O3摩擦体系的摩擦系数和磨损率均出现了明显降低,表明高p H值溶液提供了良好的润滑性。此外,OH-比Cl-具有更好的亲和力,因此高p H值有助于改善材料的局部腐蚀。腐蚀磨损过程中,机械磨损面与钝化区形成了电偶腐蚀,而p H值的升高则减轻了材料的腐蚀损伤,导致机械磨损和腐蚀对磨损的促进成为材料的主要损伤原因。因此,提高腐蚀性溶液的浓度和p H值,如增加海水中氯离子浓度和p H值,均可大幅度降低腐蚀磨损过程中的纯机械磨损和腐蚀对磨损的促进作用,该研究可为金属材料的耐磨抗蚀提供新思路。
牺牲阳极法阴极保护是一种获得广泛应用的腐蚀防护技术,通过给被保护金属材料施加一个阴极电流,而给辅助阳极施加阳极电流,构成一个腐蚀电流的方法为强制电流法。因此,外加电位同样可以用于材料的腐蚀磨损防护,而适宜的外加电位则是该方法的关键因素[26-28]。研究表明:当外加电位低于钝化膜的点蚀电位时,因腐蚀磨损的交互作用,使材料的总损失显著增加;当外加电位高于点蚀电位时,材料的腐蚀被抑制,因此材料损伤为纯机械磨损。最终,材料的耦合损伤结果表明,机械磨损和腐蚀对磨损的促进同样在材料损伤中占主导地位。因此,材料的腐蚀磨损耦合损伤与其磨损抗力密切相关,提高材料的硬度、韧性等力学性能,如选择高耐磨材料、表面改性等,均有望显著提高材料的耐磨抗蚀能力。
材料的本征物性,如硬度、耐蚀性、耐磨性等是影响材料腐蚀磨损性能的关键因素[29]。因此,对比不同金属材料(如不锈钢、钛合金、镍合金、铝合金等)的腐蚀磨损性能,可为涉海环境服役装备的选材提供技术支撑。
表1为不同金属材料的腐蚀磨损测试结果。通过表1可知,奥氏体不锈钢比马氏体不锈钢更适合用于腐蚀性海水环境的运动部件,可提高不锈钢的耐氯离子腐蚀抗力,如316L不锈钢与304不锈钢相比,能显著降低腐蚀损伤,腐蚀加速磨损损伤明显下降。此外,铁素体和奥氏体的2205双相钢相比单一奥氏体不锈钢,可进一步提高零部件的腐蚀抗力,进而延长零部件在腐蚀性介质中的服役寿命。例如,304不锈钢的腐蚀加速磨损损伤约为材料总损伤的20%,而2205双相钢为11.6%,因此,提高耐腐蚀性可显著降低不锈钢材料因腐蚀、腐蚀加速磨损的损伤。对于不锈钢和钛合金而言,钛合金具有更优异的耐磨抗蚀性能。但是,钛合金的腐蚀加速磨损损伤约为材料总损伤的37%,表明腐蚀是导致钛合金磨蚀总损伤的关键因素。对于铝合金,机械磨损损伤占材料总损伤比约为98.1%~80.2%,显著高于不锈钢及钛合金等材料,成为导致铝合金磨蚀失效的关键因素,因此提高耐磨性是铝合金应用于腐蚀介质运动部件的首选处理方法。相比钛合金和不锈钢,镍合金从力学性能和耐腐蚀性两方面提高了材料的耐磨抗蚀性能,更加适用于严酷腐蚀环境下的运动部件。
表1不同金属材料的腐蚀、磨损及其交互作用对比关系[23.27,30-33]
Tab.1 Comparison and contrast of corrosion,wear and interaction of different metallic materials
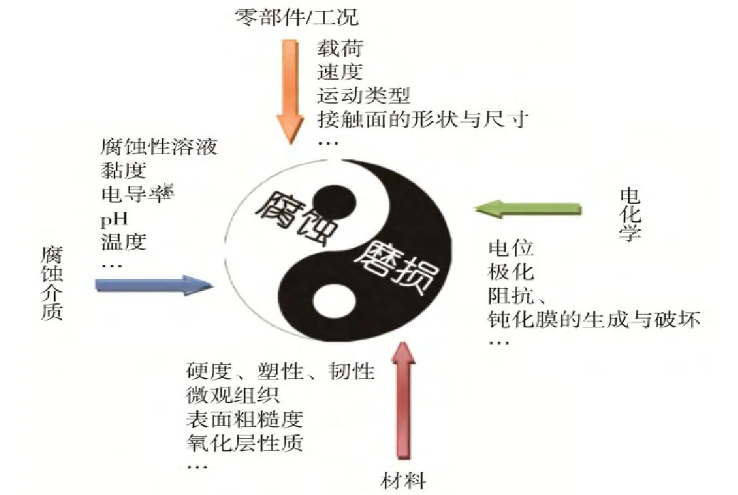
综上,对于以不锈钢为主的金属材料,传统结构材料的低硬度制约其抗磨能力,导致机械磨损在腐蚀磨损中占显著地位,如316L不锈钢和2205双相钢的机械磨损约占总损失量的70%,钛合金、镍合金、铝合金的机械磨损分别约占总损失量的63.7%、71.5%、80.2%。因此,在不降低材料耐腐蚀性的前提下,提高金属材料的硬度是改善其耐磨蚀性能的有效手段。