不同于预腐蚀疲劳,腐蚀疲劳是材料及结构在腐蚀介质与循环应力的联合作用下发生的一种不可逆损伤行为,其研究目的之一是预测材料及结构的使用寿命,而探明腐蚀疲劳机理是预测腐蚀疲劳寿命的基础与关键。本节简要论述了金属材料的腐蚀疲劳失效机理研究。
在蚀坑萌生阶段,金属材料的不连续处会优先发生电化学反应而成为腐蚀坑形核的位置,例如夹杂物、气孔或孔洞、晶界等[13,14,15,16]。然而,腐蚀坑的形成不仅取决于溶液和金属表面的电化学状态,还与材料的受力状态及表面残余应力有关[17,18]。研究发现,外加应力越大,金属表面腐蚀坑的数量越多[19],并且循环载荷作用下的蚀坑横截面面积是恒载荷或无载荷作用下蚀坑横截面面积的三倍[9],根据图像灰度值分析对比发现,交变应力作用下的腐蚀率大于无应力工况和静应力工况的腐蚀率[20],可见外部载荷会加速蚀坑的形核与生长。
金属在腐蚀介质中发生的电化学反应包括阳极溶解和阴极反应两部分,简要概括如下:
阳极溶解:M→Mn++ne-
阴极反应:{2H2O+O2+4e−→4OH−2H++2e−→H2
水解反应:Mn++nH2O→M(OH)n+nH+
由阳极反应产生的金属阳离子可发生水解反应或与腐蚀阴离子结合产生沉淀形成保护膜,阻止周围金属的溶解,但无论由哪种反应产生的H+都会使点蚀坑内的局部pH值降低,这种“自催化”效应进一步促进点蚀坑的生长。
相较于点蚀阶段,腐蚀环境中的开裂现象主要由疲劳载荷主导。金属材料的腐蚀疲劳裂纹萌生机理主要有[21,22,23]:①蚀坑应力集中理论:点蚀坑处的应力集中促进了裂纹萌生,但不适合点蚀不敏感材料;②滑移带优先溶解理论:交变载荷作用下变形区出现滑移带,相对未变形区为阳极进而优先溶解形成疲劳裂纹;③保护膜破裂理论:金属表面的保护膜在外力作用下产生破裂,暴露的金属与保护膜覆盖部分形成原电池。裸露金属作为阳极发生溶解,直到保护膜再次被修复,如此重复导致疲劳裂纹萌生;④吸附理论:金属在腐蚀介质中吸附活性物质,表面能下降,在疲劳载荷作用下萌生裂纹。
蚀坑应力集中理论是较早被提出也是较为常用的疲劳裂纹萌生机理解释方法,适用于大多数金属材料的腐蚀疲劳裂纹萌生行为。然而,一些金属材料在未出现点蚀时依然有裂纹萌生[24],说明点蚀并不是裂纹萌生的必要条件。因此,同属于阳极溶解的滑移带优先溶解理论和保护膜破裂理论很好的解释了点蚀不敏感的不锈钢和铝合金等易钝化金属的裂纹萌生行为。此外,氢脆作为吸附理论的典型例子,也是解释金属疲劳裂纹萌生机理的常用理论[25]。
裂纹萌生后在交变载荷与腐蚀介质的共同作用下继续扩展,研究认为腐蚀疲劳裂纹的扩展机理与应力腐蚀开裂机理类似,包括氧化膜破裂-阳极溶解、氢致开裂和二者的混合机制[26,27,28]。但无论是合金材料的自身属性还是腐蚀介质的种类都会引发不同的失效结果,所以目前尚不存在任何一种普适性机理解释腐蚀疲劳裂纹的扩展行为。
氧化膜破裂-阳极溶解理论认为裂纹尖端在交变载荷作用下发生局部塑性变形产生滑移台阶,且存在高密度的位错和变形而处于电化学活跃状态,相对于未发生破坏的区域发生阳极溶解造成局部钝化膜的破坏,因此进一步促进裂纹的扩展。氢致开裂理论认为氢在裂纹尖端的吸附会诱使氢原子迁移至金属内部,降低金属原子间的作用力促进位错的运动,使尖端出现局部高应变区,促进裂纹的快速扩展。随着研究的深入,其他氢损伤理论也被提出,如氢压理论、氢脆理论、位错输送理论、氢降低原子间结合力理论和氢促进局部塑性变形理论等[21,28,29],进而解释不同材料的腐蚀疲劳裂纹扩展机理。然而,在溶液环境中金属材料的腐蚀疲劳机制一般以阳极溶解和氢致开裂的混合机制为主。混合机制认为氢原子迁移至裂纹尖端后促进阳极溶解,二者相互依存,这也符合上文的氧化还原反应原理。
与恒定载荷相比,交变载荷存在加、卸载过程,因此腐蚀疲劳裂纹在扩展过程中存在裂纹闭合效应。裂纹闭合效应会引起裂纹尖端有效应力强度因子的变化,进而影响裂纹的扩展。腐蚀疲劳裂纹闭合理论主要有:塑性变形机制、裂纹路径粗糙理论和腐蚀产物堆积理论[30]。在交变应力卸载过程中,由于腐蚀疲劳裂纹的扩展路径曲折、偏转或存在腐蚀产物的膨胀与堆积,造成裂纹尖端处的应力水平未下降到预设值,从而导致有效应力强度因子的降低,阻碍了裂纹的扩展。
目前,针对腐蚀疲劳裂纹扩展机理的研究一般采用扫描电镜、电子背散射衍射技术、电化学试验等二维、静态和破坏性的传统表征手段[25,27,31,32],通过观察断口、腐蚀坑形貌、裂纹扩展路径、裂尖位错形态以及电化学行为等方式,进而反推材料的腐蚀疲劳失效机理。然而,由于难以准确获取腐蚀坑形貌及空间动态演化尺寸,一些重要的实验现象可能被忽略,例如金属夹杂物对局部腐蚀的加速[13],氢气的产生位置及扩散路径[14],裂纹尖端的形态演变及微观结构与裂纹的连通行为[15]等。因此,有必要利用三维成像技术进行腐蚀疲劳可视化研究,实现进一步的失效机理解析。
Bernabale[33]借助X射线显微镜(X-Ray Microscopy, XRM)观测锈蚀钢钉的整体腐蚀情况,获得了内部不连续结构和腐蚀物相的分布图像。Burnett[34]利用XCT成像获得石油管道钢在盐水环境中腐蚀坑随时间的形核和增长的动态过程,并观测到点蚀与晶间腐蚀的竞争现象。Turnbull[35]通过X射线计算机断层扫描(X-ray Computed Tomography, XCT)技术实现蚀坑和裂纹的三维可视化研究,观察到静态应力场中不断增长的蚀坑处存在多个裂纹,如图2所示。Stannard[13]利用高分辨率同步辐射光源原位观察腐蚀疲劳裂纹扩展行为,如图3所示,揭示了7075铝合金腐蚀疲劳裂纹扩展过程中氢气的扩散路径。俨然,借助先进的X射线成像技术实现对微观结构演变、氢气扩散、裂纹扩展等现象的三维可视化观测,有助于进一步揭示腐蚀疲劳失效机理。
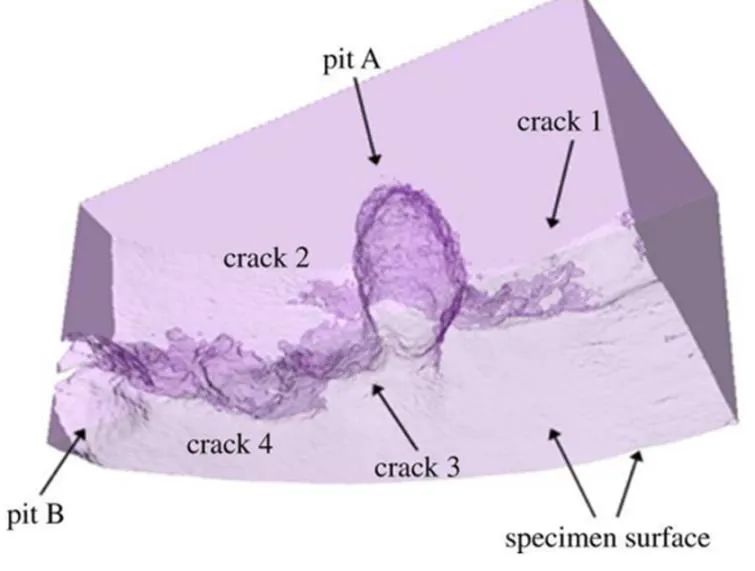
图2 腐蚀坑和裂纹的XCT成像图[35]
Figure2 XCT imaging of corrosion pits and cracks
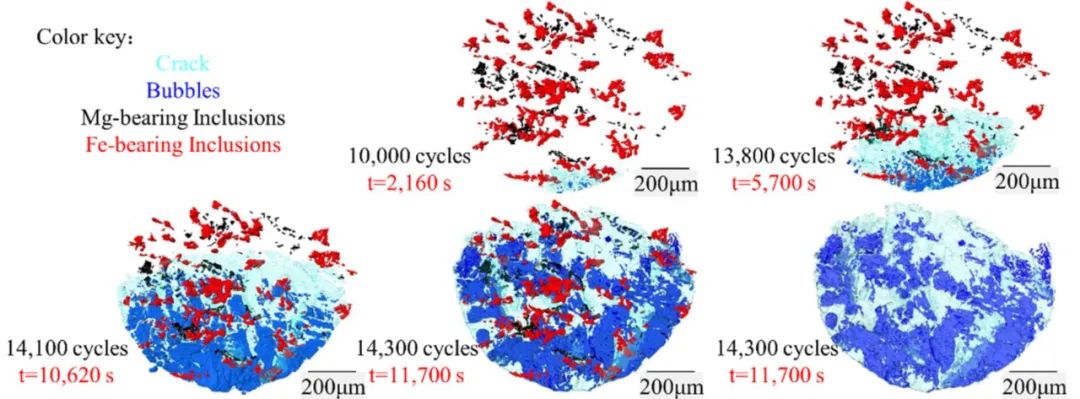
图3 峰值时效老化样品中自上而下的疲劳裂纹渲染图,图示裂纹沿L-T平面扩展,浅蓝色为裂纹,深蓝色为氢气泡,黑色为含镁夹杂物,红色为含铁夹杂物[13]
Figure 3 Top-down renderings of the fatigue crack in the peak-aged sample showing the crack progressing approximately along the L-T plane in light blue, gas bubbles in dark blue, Fe-bearing in red, and Mg-bearing inclusions in black
除借助高精度工具对试验现象进行观测外,定量模拟也是进行机理探索的一种常用手段。裂纹的萌生和扩展实质是在分子或原子尺度上发生的物理现象,因此有必要借助纳观模拟方法进行机理探索。分子模拟利用计算机建立分子或原子体系,在原子水平上模拟物理现象,通常包括量子力学方法、分子力学方法、分子动力学模拟方法和蒙特卡洛模拟方法[36]。尽管量子力学方法可预测性较强但仅能模拟数量为1000左右的体系且计算量大,应用具有局限性。在处理更大的体系模拟问题时可以采用其他三种非量子力学模拟方法来降低计算成本,然而分子力学法常被用于解决稳态体系问题,不适用于腐蚀、裂纹扩展等与时间相关的动态体系模拟。相较于分子动力学,蒙塔卡罗模拟仅能获得系统的统计平均值,在获取体系动态信息方面能力有限。因此分子动力学(Molecular Dynamics, MD)是目前模拟复杂系统特性的常用手段,也是模拟环境作用下裂纹扩展特性的有效手段。
MD在研究环境作用下的裂纹扩展及腐蚀过程中发挥了极其重要的作用。Kallikragas[37]采用MD进行了高温高压下腐蚀过程模拟,获得了实验无法获得原子迁移现象,探究了水在腐蚀层纳米裂纹中的移动。Song[38]采用分子动力学模拟研究氢原子对α-Fe裂纹扩展的影响,证实了氢浓度的增加会促进原子热运动增强晶格畸变,并且通过模拟发现裂纹扩展过程中,位于裂纹尖端直前方的氢原子趋向于向滑移面和裂纹尖端处移动,该模拟为抗脆断材料的设计提供了参考。Yasbolaghi[39]将MD用于循环载荷作用下单晶和多晶结构的裂纹扩展行为的微纳米尺度研究,为材料的宏观断裂失效提供依据,模拟结果如图4所示。Elapolu[40]利用MD模拟研究石墨烯应力腐蚀开裂机理,分别采用单一的MD模拟和MD模拟结合基于密度泛函的紧密键合(Density Functional-based Tight Bondin, DFTB)两种方法(见图5),模拟结果有助于对应力腐蚀开裂过程中裂纹尖端处微观行为的研究。盛鹰[41]等将MD模拟与有限元方法(Finite Element Method, FEM)结合提出多尺度建模方法,实现宏观载荷作用下微观裂纹扩展过程的动态数值分析,模拟裂纹扩展和裂尖变形的多尺度演化过程。综合来看,MD模拟或许可以成为探索金属材料腐蚀疲劳失效机理的可用方法。
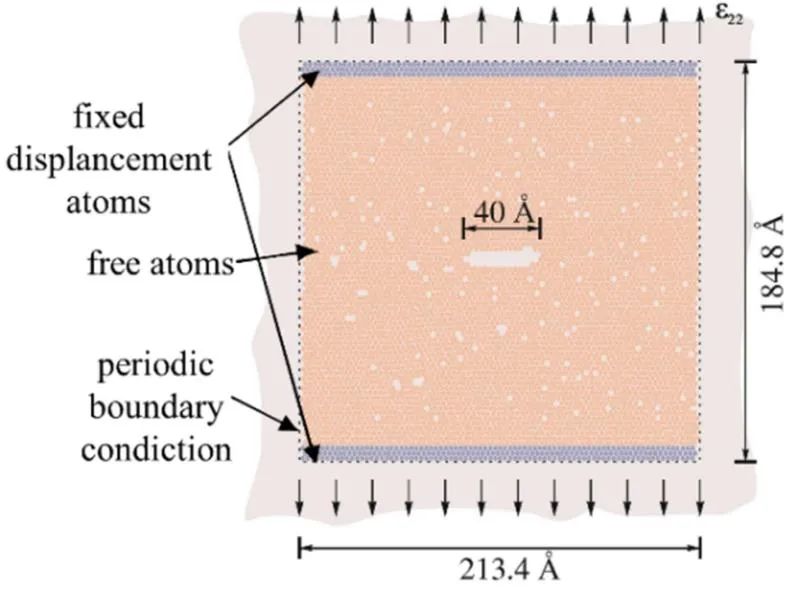
(a) I型加载条件无限裂纹区(a) An infinite cracked domain subjected to mode I loading condition
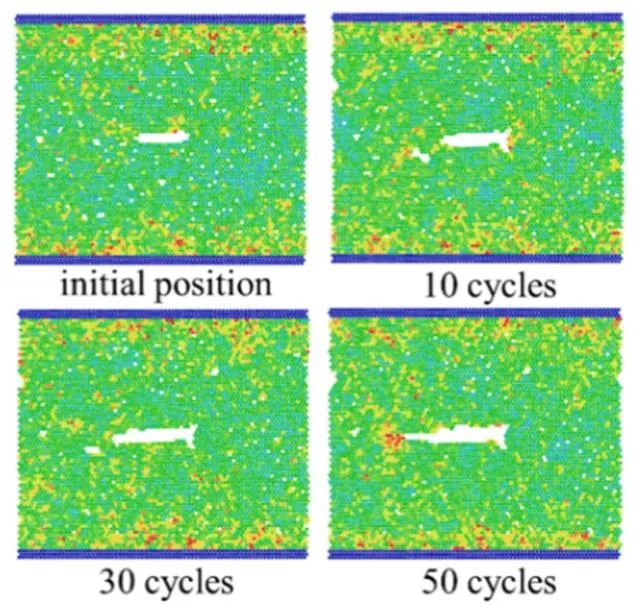
图4 MD模拟循环载荷作用下单晶缺陷I型裂纹扩展[39]
Figure4 MD imulation of single crystal defect type I crack propagation under cyclic loading[39]
(b) 循环加载下裂纹扩展过程(b) Fatigue crack propagation due to cyclic loading
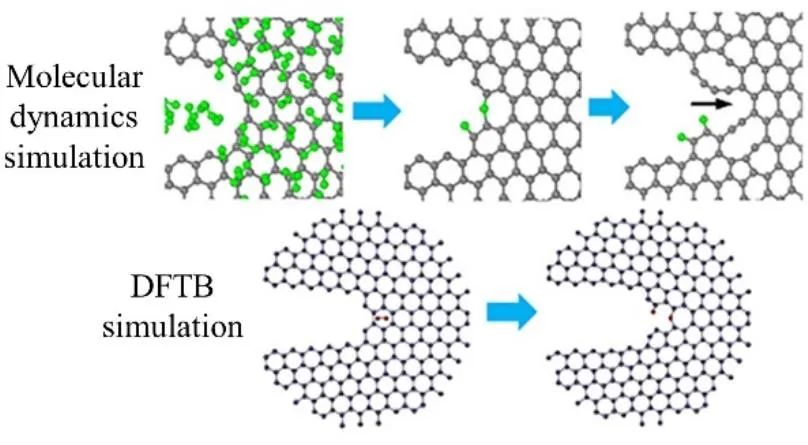
图5 预应力石墨烯薄片与O2分子之间的化学反应过程[40]
Figure 5 Chemical reactions process between a prestressed graphene sheet and O2 molecules[40]