失稳氧化的机理
失稳氧化的机理
失稳氧化导致氧化膜出现大量裂纹,氧化膜中的裂纹为氧扩散提供了短路通道,该通道成为主要的氧扩散路径。
关于失稳氧化和裂纹产生的原因,目前业内持不同的观点。其中一种主流观点认为它与氧化膜中t-ZrO2转变成m-ZrO2的相变有关。
锆合金的氧化物ZrO2通常有三种晶体结构:低温稳定的单斜相(monoclinic,m-ZrO2)、1205℃以上稳定的四方相(tetragonal,t-ZrO2)和2377℃以上稳定的立方相(cubic,c-ZrO2)。在无应力状态下,t-ZrO2相转变为m-ZrO2相的温度为1150℃。t-ZrO2相主要分布在O/M界面,这是因为锆氧化生成氧化锆的PB比(ZrO2中Zr离子与金属Zr中Zr原子的体积比)为1.56,在形成的氧化膜中产生很大的压应力,压应力使得t-ZrO2相稳定;m-ZrO2相主要分布在远离O/M界面的位置。
LEISTIKOW等认为发生失稳氧化的标志是平坦的O/M界面变为波浪状表面,波浪状表面导致氧化膜局部出现拉应力和压应力,部分区域的氧化膜在拉应力的作用下从t-ZrO2相转变为m-ZrO2相,m-ZrO2相力学性能差,容易开裂,蒸汽通过裂纹直接与内层金属基体反应,氧化速率增加,吸氢加速。
LEISTIKOW等提出的失稳氧化机理与锆合金在高温高压水中腐蚀发生氧化转折(氧化动力学规律发生变化)的机理基本相似。虽然大量试验发现氧化转折后,t-ZrO2相转变成m-ZrO2相,但是LOCA工况下发生的失稳氧化现象与t-ZrO2→m-ZrO2相变之间的关系至今还没有实验依据。
YAN等认为E110合金之所以具有与其他合金不同的失稳氧化行为,主要与表面粗糙度、杂质等因素有关。E110合金是由精细Zr电解液制得,电解过程去除了杂质,单电解液中加入氟化物,氟化物污染对腐蚀有不利影响。
KIM等选取Alloy-A和Zr-4两种合金材料开展了模拟LOCA工况下的高温蒸汽氧化,结果发现失稳氧化后α-Zr(O)中氢化物与氧化物的分布几乎同步,如图1所示。因此推测失稳氧化与α、β相稳定剂及氢化物分布有关。
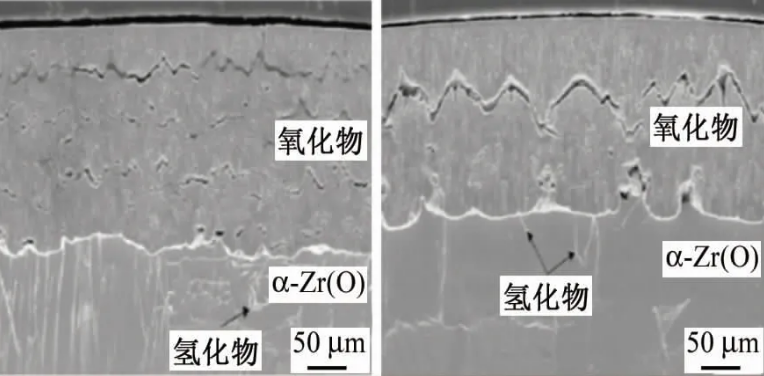
(a) Alloy-A合金 (b) Zr-4合金
图1 氧化5000s后Alloy-A和Zr-4合金表面氧化膜的SEM图
在此基础上,他们提出了另一种失稳氧化机理:当β相稳定剂含量较高时,氧化产生薄片状的α-Zr(O),由于α-Zr(O)晶界多,在氧化物/α-Zr(O)界面处的氢较易进入早期β相,因此冷却至室温后,α-Zr(O)相中几乎没有氢化物;当α相稳定剂含量较高时,形成块状的大晶粒α-Zr(O),聚集在界面处的氢很难进入早期β相,冷却后在α-Zr(O)晶界处有氢化物析出。
图2为氢诱发失稳氧化机理示意。在Alloy-A合金表面,α-Zr(O)的晶粒形貌复杂,既有薄片状,也有块状,也就是说Zr的基体材料中既含α相稳定剂,又含β相稳定剂,在薄片状α-Zr(O)处,氢可扩散进入早期β相,在块状α-Zr(O)处,氢被束缚在氧化物/α-Zr(O)界面和α-Zr(O)晶界处,此处氢气压力随着氧化时间的延长而增大,直至氧化层开裂,表面形成白色的疖状腐蚀物,表现为白点。在Zr-4合金表面,由于氢气产生的压力逐渐增大,导致氧化层性能下降,进而产生了波浪状表面。形成疖状表面还是波浪状表面主要取决于氧化层厚度,若氧化层薄,氧化层性能全面下降,表现为疖状表面,若氧化层厚,氧化层性能部分下降,表现为波浪状表面。由于合金元素会影响α-Zr(O)的晶粒尺寸,从而影响失稳氧化,因此失稳氧化与合金元素也有一定关系。
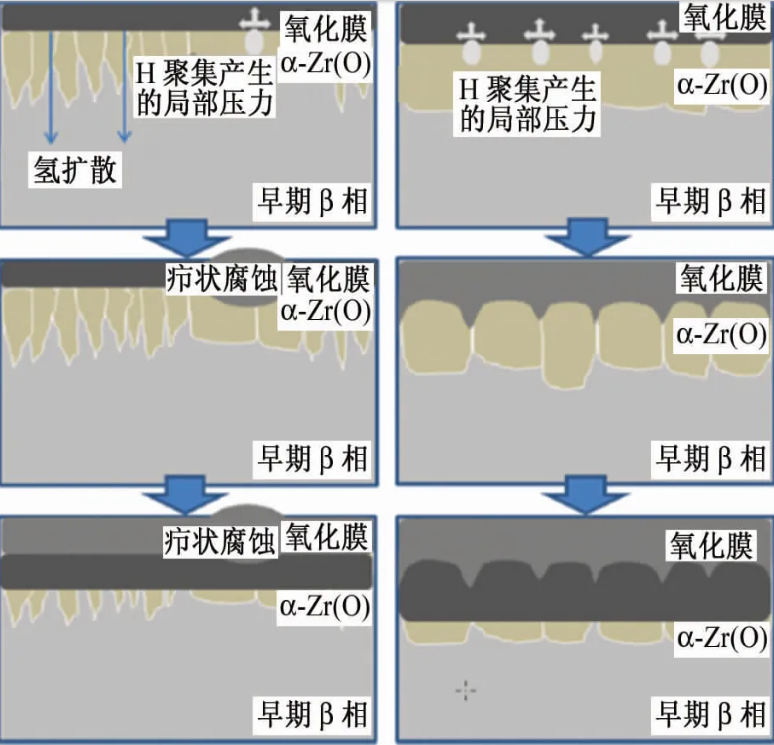
(a) 疖状表面 (b) 波浪状表面
图2 氢诱发失稳氧化机理示意
转载请注明精川材料检测地址:www.jctest.vip